Columun
Kiso Shikki Kiso Lacquerware
Harunoya Lacquerware Studio
Master Lacquer Craftsman
Mr. Hiroyuki Kobayashi
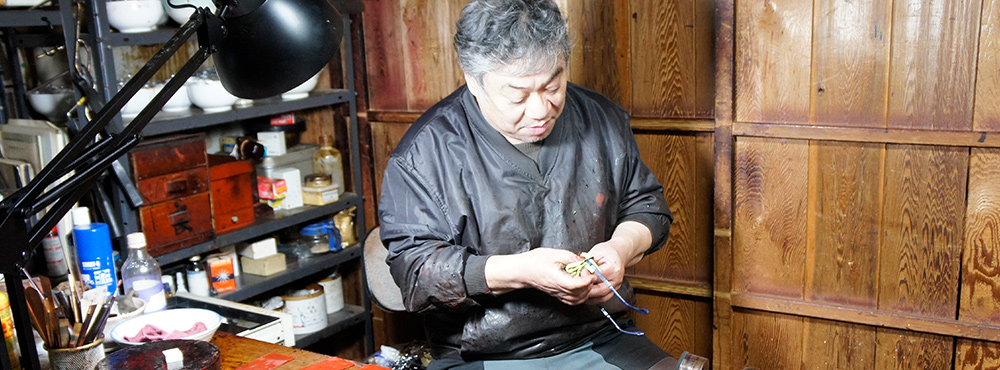
Neat displays of bowls, lunch boxes, and other objects greeted us with their lustrous coatings of warm brown, vibrant red, and even a deep sky blue. In a second floor workshop, a narrow space void of windows, Mr. Hiroyuki Kobayashi sat in front of closeted shelving, which we learned was filled with drying pieces of lacquerware. He began by giving us a friendly warning that we would need weeks to hear the entire backstory on lacquer. As he spoke, he revealed a good sense of humor and a modest, but earnest personality. He is continuing in his grandfather’s footsteps, but his dedication to keeping the tradition alive has made him open to change. He hopes to interest people outside of Japan in Japanese lacquerware. He gave us background on Kiso’s lacquer industry, details on the varnishing process, and his thoughts on the future of lacquerware.
History
Japanese lacquer dates back thousands of years. It is produced with resin from the urushi tree and thus called urushi in Japanese. Kiso’s primary industry was forestry and woodworking due to the area’s abundant supply of timber including the renowned Kiso-hinoki cypress. With these resources, lacquerware production was a natural undertaking. Kiso’s lacquer style originated in Kyoto, but after a key type of clay used in the varnish was discovered in the local area, Kiso lacquerware boomed.
You’ll find many different hues of lacquer in Kiso. While the black and red dyes are probably the most well-known, you will also find styles here that leave the wood grain beautifully exposed. In the past, the vibrant coloring was produced with toxic materials including mercury and arsenic. Laughing, Mr. Kobayashi reassured us by saying that one of the craftsmen is 80 years old and doing just fine.
Kiso’s lacquerware industry was a bit of an anomaly in that craftspeople were not making pieces on behalf of the shogun. Furthermore, Kiso was located on the Nakasendo Road (internal link?), which was a major route connecting Kyoto and Edo (present day Tokyo). Lacquerware made for a good souvenir, so the industry flourished.
Lacquering Process
Speaking while he worked, Mr. Kobayashi revealed the dedication that goes into making the hand-lacquered items. The arduous process requires strict working conditions to keep dust and other tiny particles from landing on the coating. Anything that does land on the surface has to be carefully picked off with a sharpened quill. Fan and heater use is kept to a minimum, but the weather itself can affect how a piece turns out.
The lacquer is carefully strained before each use to get out any foreign particulates. Pieces require multiple coats that take three to four days to dry each. The drying conditions, including humidity, must be strictly regulated, since drying speed determines how strong the finished lacquer coating is.
Other traditional and extremely rare tools remain. He showed us one of his brushes called kamoji that had a stiff, almost wood like texture. It turns out the brush was made from human hair. Now, only four people who can make the brushes are left in Japan.
While high quality lacquerware is not cheap, know that if it is properly cared for, it can be used for over a hundred years. Since lacquer contains high levels of natural acid and oil, it is highly resistant to water, bacteria, and acid. It can also withstand high temperatures to a certain degree. Lacquerware can truly be considered a timeless craft. It is said that it can even make its contents taste better!
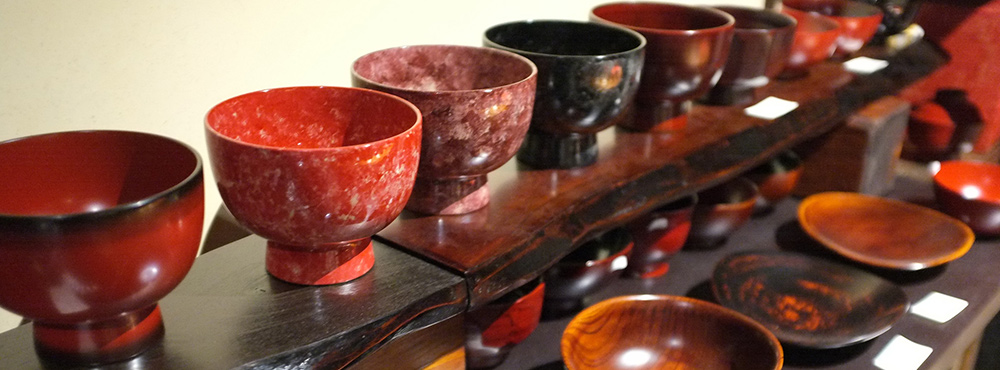