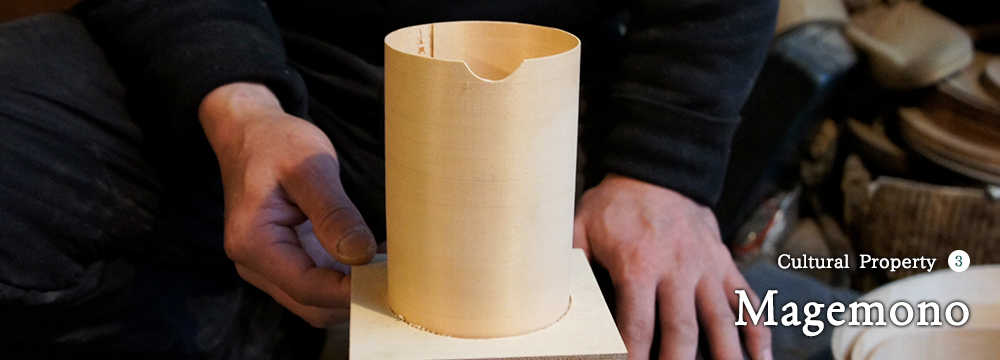
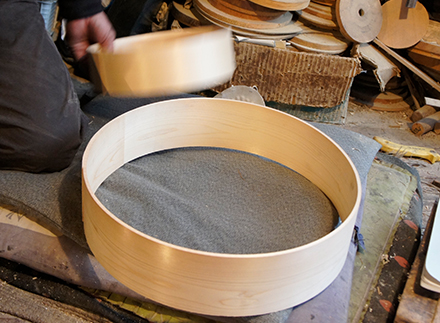
Story
Utensils for soba making and tea ceremony are made by immersing shavings from Kiso-hinoki cypress in hot water so they bend.
Overview
Magemono is plateware made by bending a thin cypress board into a circle or oval, fastening a seam with the bark of a mountain cherry tree, and adding a bottom.It has a history of over 400 years and has been integrated into the everyday lives of the Kiso people. The lightweight, sturdy, and easy-to-use plateware is a popular traditional craft even in modern times.
Points of Interest
The Kiso Lacquerware Museum and Kiso Kurashino Kogeikan Museum display and sell magemono.
Interview
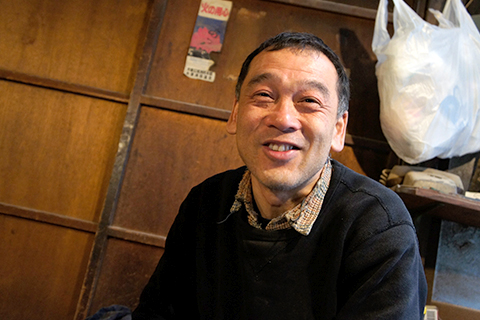
Takayuki Kojima, from Magemono Cooperative
Magemono has a history of more than 400 years. Magemono is plateware made by bending a thin cypress board into a circle or oval and fastening a seam with bark of a mountain cherry tree and putting a bottom. We interviewed Mr. Takayuki Kojima. He has inherited the tradition and belongs to Magemono Cooperative.
“It is said that people started to make a living with magemono techniques in the Edo period.
At that time, lumber was in high demand everywhere for use in construction. Kiso-hinoki cypress was valued as the best material in Japan.
A strict forest preservation policy was enforced to protect the Five Trees of Kiso, as summarized by “a head for a cypress, an arm for a branch.”
“In addition to the Kiso Valley, the Nagawa area was administered by the Owari Domain, not by the Matsumoto Domain. That’s why the Nagoya dialect can be heard in Kiso. Logs were sluiced down the Kisogawa River to the Owari Domain. The logs were collected in Nagoya, assembled into large rafts, or carried to Edo by ship. Kiso made huge profit as a leading producer of wood.
Local products were encouraged, and all the woods were made into woodcrafts in Kiso to sell nationwide. Because of the woodcrafts, lacquerware was introduced.”
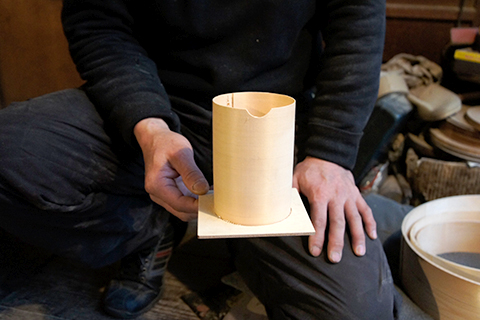
Bending wood
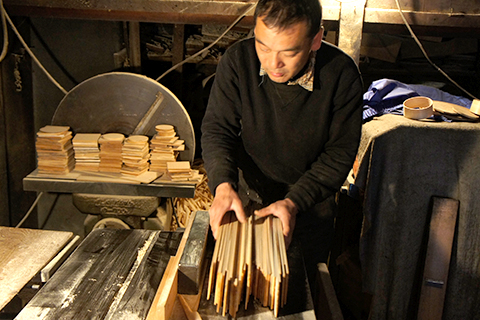
Wood materials
“I heard my ancestors came from Takayama, Gifu. The techniques of magemono and comb-making came down with them.
I took over the family business because I liked making things.” he continued. He was painting lacquer when he was eighteen, but he got into woodcrafts after his father died.
“It is hard to buy wood materials nowadays. I use hinoki cypress for the side and sawara cypress for the top and bottom. Sawara makes up for hinoki’s flaws and is highly waterproof. I put a thin board in a tubful of hot water to make it soft and bend it using a wood-burning stove.”
Bending a thin board without breaking it requires proficient skills.
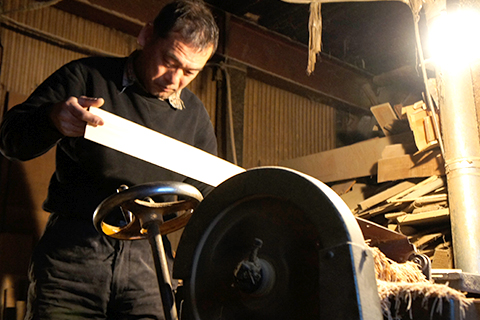
Work scene
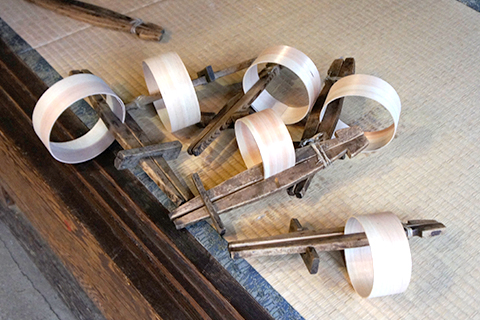
Bent boards
“Pieces made from Kiso-hinoki cypress are just gorgeous.
After you use magemono, you will realize how good it is. Some people come back to us to have their long-used magemono repaired after several decades. It keeps well for a long time.
Put some rice in magemono, and the rice will keep well. And wood is highly bacteria-resistant. Just visit us to pick up magemono and appreciate them.”
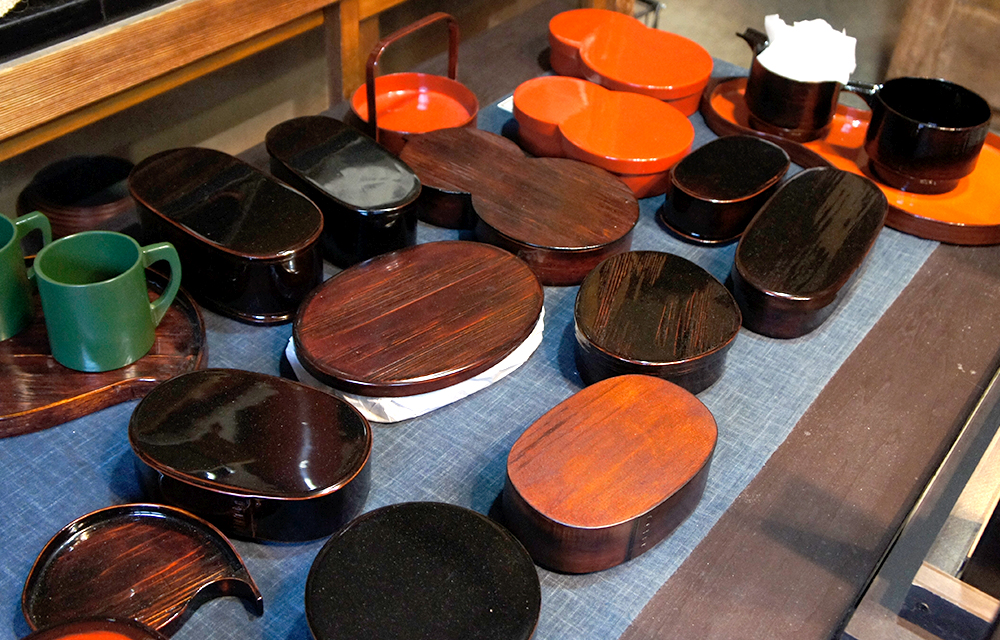
Magemono works
“I wish to pass the techniques on to the next generation.
I often tell tourists that I never conceal any techniques. Anyone is welcome to see them.
I made light of the work at first, but now I find it enjoyable. I’m fortunate to have something to work on for the rest of my life.
I hope that many people will see my crafts and techniques while I live.
I wish to teach on the spot and to continue making traditional things without fail. It is my desire to make such things popular,”
Mr. Kojima said earnestly.
Attractions
The Kiso Lacquerware Museum and Kiso Kurashino Kogeikan Museum display and sell magemono.
Access
From the closest station & interchange
From Kiso Hirasawa Station on the JR Chuo Line
5 minutes’ walk
From the Ina Interchange on the Chuo Expressway
From the Ina Interchange on National road 361, 30 minutes by car
From the Shiojiri Interchange on Nagano Expressway
National road 19, 30 minutes by car
Address
Kiso Lacquerware Museum
2324-150 Kiso Hirasawa, Shiojiri City, Nagano Prefecture
Phone:0264-34-1140